I've resisted posting these details because I didn't want to break Neander rules, but I'd just hate to think of someone buying manufactured jigs when it's so easy to get perfect results cheaply.
Or you could make an absurdly cheap, ridiculously simple, and awesomely effective jig from scraps or cheap sheet goods. When I started out with power tools I felt deprived when I realized there was no way I could fit a table saw and its noise and mess into my little apartment and front porch, and just as discouraged when I considered spending precious $$ on manufactured jigs--until I discovered that
this jig meant I didn't need any of it.
Right away I was making straight, square, clean cuts using the jig, a DeWalt 18V trim saw, a Diablo 140 tooth OSB/plywood blade, and a 12" strip from the factory edge of a sheet of 1/4" tempered hardboard. Any stable material will work
so long as the guide edge of the top piece is dead straight, which is why I used the Masonite's factory edge (after checking it with my best straight edge).
To use it, line the jig's edge up with your cut line, make sure it's square to the edge of the workpiece with either a square or a batten attached to the bottom of one end, clamp the jig to the workpiece, and cut away. No measuring to add the width of the saw plate; in fact, you only need to make one mark for your cut and then square the jig to the mark, although it was easier to use two marks.
Here's the main part of the wayneofthewoods.com plan, edited for brevity:
Step 1 - Get a 12-inch wide piece of 1/4" to 1/2" plywood (1/4" to 1/2" ) that is the desired length of the type of cuts you will make, usually 4 or 8 feet.
Step 2 - Obtain another 2-inch wide board or strip of plywood with one long edge that is dead straight. It must be thin enough so that the body of the saw will clear it when your circular saw rests up against it. This will be your guide strip.
Step 3 - Fasten the guide strip onto the plywood. Leave an inch or two behind the guide to clamp the guide to the workpiece, and make sure the strip's straight edge is facing the side to be cut.
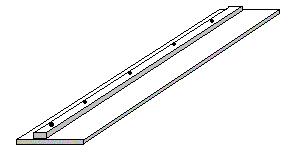
Step 4 - Rip your plywood with the saw resting against the guide strip's straight edge.
My tips:
* A coat or two of furniture wax on the surfaces the saw slides against will help its plate glide smoothly.
* Smooth off any rough edges on the saw plate with fine sandpaper and wax it, too.
* Stick some PSA backed sanding disks to the bottom of the jig to keep it from sliding around.