Ray,
I personally am not too fond of the mini-mill, but it does work, and I give credit to folks who use them, I would have not thought you could use it for doing this, and several machinist friends of mine advised me against it, after all they do have plastic gears! They really need to be taken apart, have the cosmoline cleaned off of them, and oil/lubed properly. Then if you add the belt drive, they can be usable, but there is all types of limitations with them in doing a lot of machining...the low quality hand wheels and table screws, the speed to reposition the table, I always have to run the table from side to side to adjust my fixture, or have a difficult time getting the slotting saw in proper position...I guess it's a love/hate relationship with it for me. It is capable of doing some stuff, and it is capable to slot handsaw backs...I bought mine locally from a guy for $200 that used it to make prototypes out of plastic. He was milling small channels in plastic with 1/16", 3/64", 1/32" and similar sizes, so it didn't see a lot of use. They are what they are. A vertical mill is not the best for slotting, IMO, and the horizontal is much better for that purpose. The Nichols is a real mill, made for production work, and many of them were run 24x7, 7 days a week, for years on end...I'm not sure the mini-mill is even capable of running 24 hours.
They don't rate the saws by tpi actually, typically the amount of teeth for the circumference. The two pictured below are both .020".
Look at MSC, they have jewelers saws with high tpi, like this with 230 teeth on a 3" diameter:
(linky pic)
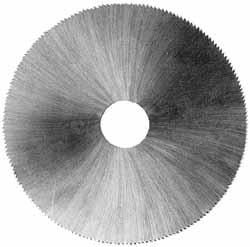
Opposed to this screw slotting saw that is 72 teeth for a 2 1/4" diameter:
(linky pic)
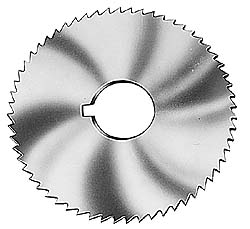
My Nichols has a 1" arbor, although arbors are pretty cheap on the used market, but a 3" blade will only provide 1" of cutting depth (less actually, because of the spacers), if you can get the arbor down to the workpiece. This is ok for saw backs, I will only go about 1/3 to 1/2 the width of the back, so 5/16" into a 3/4" width back, aprox. Again, all of our mileage varies. Maybe some of the professional saw makers can give you better data, I've only made a few saws.
Remember this is all relative also, you need to calculate the amount of teeth per the rpm of the blade in conjunction with the diameter of the blade to come up with the amount to cut, I don't have the formula off the top of my head. The mini-mill allows adjusting of 0-1700 rpm with factory plastic gears, but the belt conversion allows for 0-4300 rpm. If your patient the mini-mill is capable of a lot, but again, it is nothing like my Nichols. 
HTH,
Last edited by Alan DuBoff; 09-20-2008 at 2:19 AM.
Reason: forgot about the spacers...
--
Life is about what your doing today, not what you did yesterday! Seize the day before it sneaks up and seizes you!
Alan - http://www.traditionaltoolworks.com:8080/roller/aland/